Our Easy-Peasy Collaborative Process
First things first, we need all the deets. Fill out the form below to provide us with a better understanding of what your dream product looks like and its performance requirements. Our engineering team will review your completed form and we will promptly get back to you with next steps.
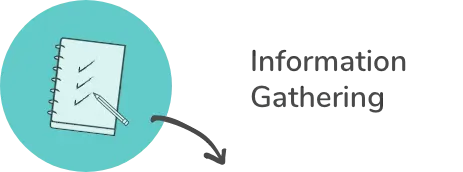
Considering we can make your (custom packaging) dreams come true, we will start the collaboration process to ensure we can deliver an end product that meets both your form and function goals (while being environmentally friendly to boot!).
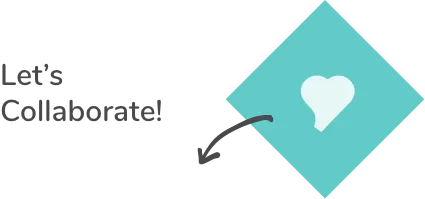
We will now start on the design and renderings of your customizable food packaging. You will have a chance to review the drawings every step of the journey. Once a final engineering drawing has been approved we will produce a prototype mold and prototype samples for you to review and approve.
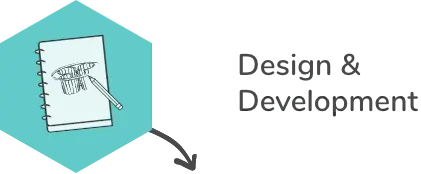

At this time we make a final product mold from the approved prototype for you to ensure everything is performing as expected. Once you approve, it's full steam ahead on our way to kicking fossil fuels to the curb with your very own custom packaging.
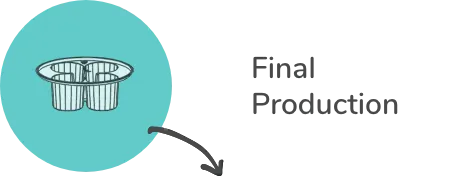
Your custom plant-based packaging is boxed up and on its way to you from one of our warehouse locations in North America.
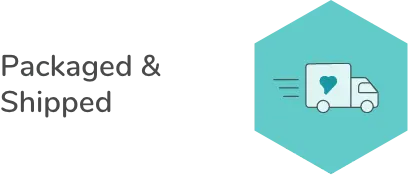
Custom Thermoformed Packaging Design
Our packaging and your product are cut out for each other, and they make the planet happier too!
The way we see it, everyone has a role to play. You delight our taste buds with the sweet stuff or the green healthy stuff … and ours is to make sure we keep your creations uuber fresh, safe and secure. We test, and test, and test (did we say test?) our products until they reach operational perfection so you can be confident they will perform equal to or greater than their fossil fuel counterparts, with no chemicals of concern!
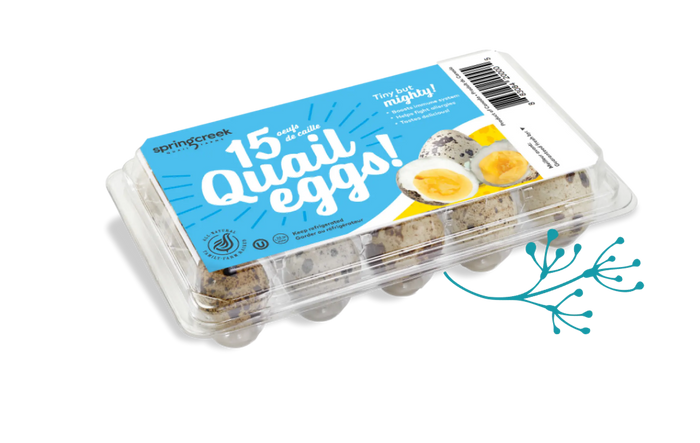
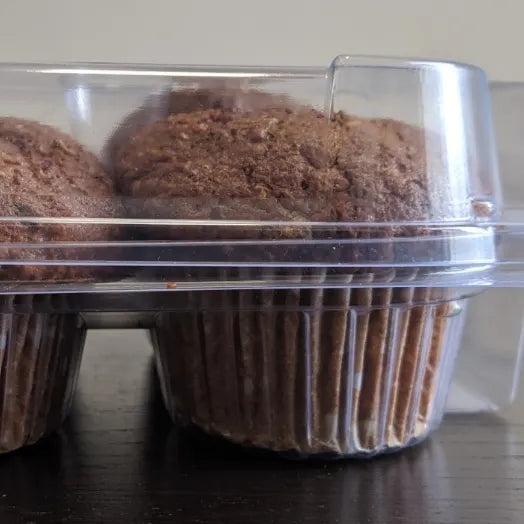
Crystal Clear Visibility
Why hide your gorgeous product behind a cardboard wall? It’s time to display them like the pieces of art they are.
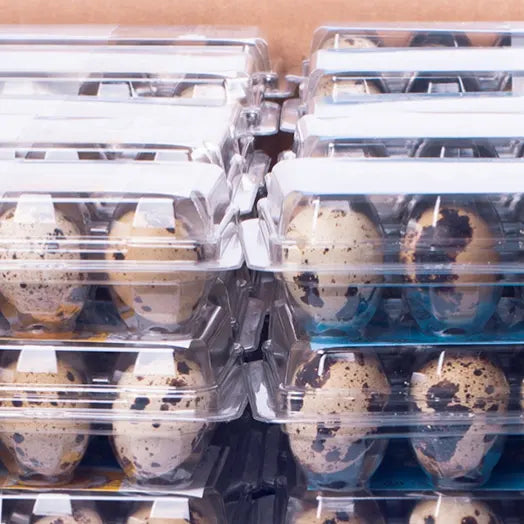
Extra Durable
Thick, sturdy design provides enhanced crush resistance for heavier or delicate items.
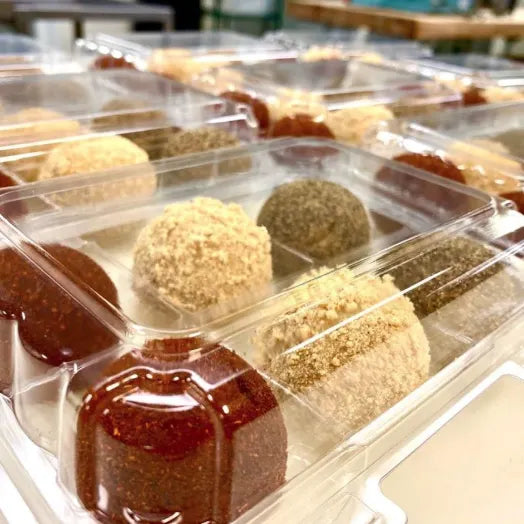
Snug Design
Hold your goods in place, without the extra packaging. Easier to ship, merchandise and more cost effective.